Using robots to eliminate high risk diving activities
For thermal assets, the cooling water system and boilers need to be inspected regularly. The use of robots prevents technicians from being exposed to high risk environments.
A combustion boiler is a key component of a thermal asset, which produces steam at high pressure to drive the turbo-generator. A combustion boiler is about 70 metres tall, equivalent to a 22-storey building, and its interior is a confined environment where regular human access is difficult. CLP is now using robots for inspection of some of its boilers. These robots are specially designed to adapt to the conditions of different boilers: some are like spiders that climb on vertical boiler tubes, others have wheels that can navigate the varied terrain. These robots can quickly detect any faults such as surface cracks, significantly reducing the time needed for inspections while improving work safety.
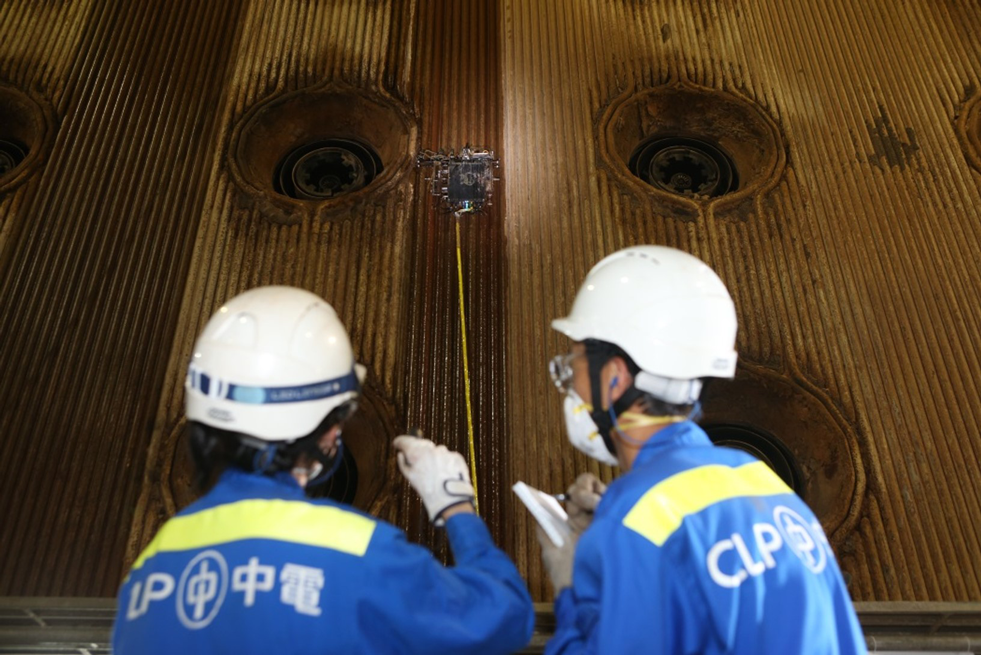
Cooling water culverts, the underwater structures that supply sea water to power generation units for cooling, are another key component that requires regular inspection and cleaning. Traditionally this was done through diving, which is a potentially high-risk activity. CLP took the initiative to use Remotely Operated Vehicles (ROVs) to replace divers for the inspection and cleaning of cooling water facilities in power plants in Hong Kong, Mainland China and Australia. The adoption of ROVs has already eliminated about 30 manned diving hours each year across the Group, in addition to shortening inspection time and reducing asset downtime.
ROVs deploy advanced technology including LED strobe lighting, imaging, underwater GPS positioning, altimeter and echosounder. CLP has worked with consultants and the Hong Kong University of Science and Technology (HKUST) to fine-tune the configurations of ROVs for application at power plants by considering water current, visibility, marine growth and complexity of works. Risk assessments were also conducted to ensure the safe use of ROVs.
Plans are now in place to further reduce or eliminate various manned diving for inspection, cleaning, maintenance, repairs and equipment installation of CLP’s marine works projects, floating solar projects, hydro plants and thermal plants by advancing ROV design changes and operational practice in the coming two years. This effectively minimises the deployment of manpower into highly hazardous underwater environments.
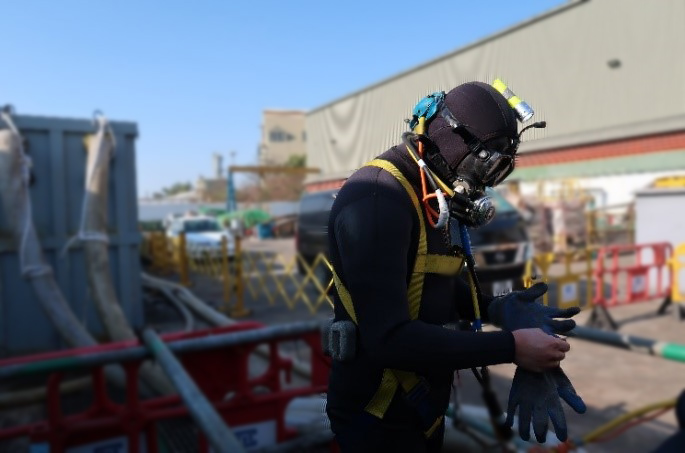
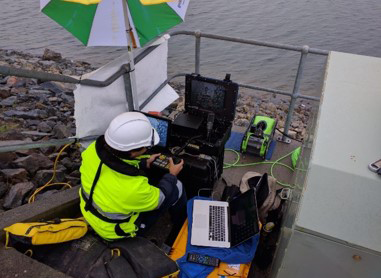
Technology improves customer services behind the scenes
Customer services are increasingly provided digitally. Application of Robotic Process Automation (RPA) helps CLP Power provide better customer experience and increased internal operational efficiency.
Customer service needs to take new forms. A CLP customer services centre was renovated and upgraded to feature multi-function self-service kiosks, deploying the latest digital technology to give customers a convenient and flexible account service and shopping experience.
During the COVID-19 pandemic, as a series of social distancing restrictions were enacted, and many of CLP’s customer service centres were not able to maintain the usual opening hours. A new mobile app was launched in April, providing customers with an end-to-end digital experience, covering services ranging from move-in services and eBill applications, to mobile payments and a Smart Shopping platform. Downloads and usage of the app saw a nearly 50% increase compared with the previous year as growing numbers of customers opted for online services.
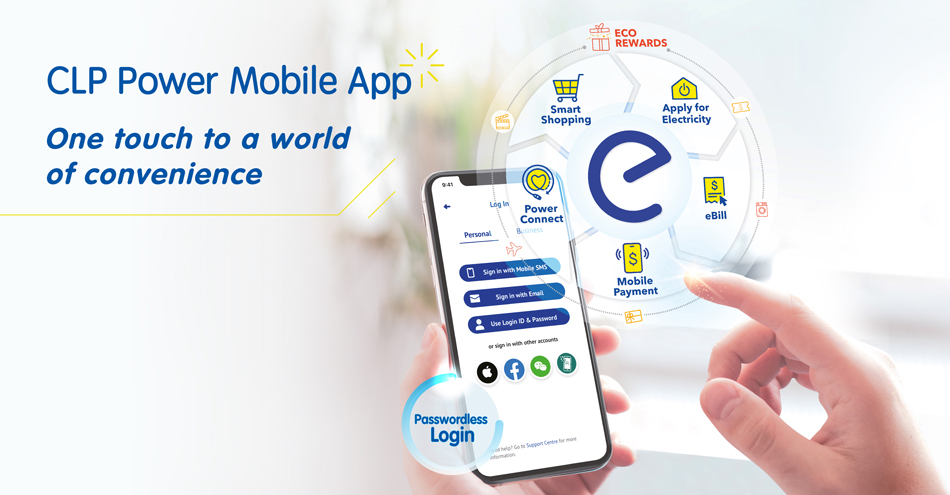
Supporting these digital services is a number of automated robotic processes to enhance its operational efficiency. RPA technology utilises computer software robots to automate rule-based, repetitive and high transaction volume business processes with high efficiency, accuracy and consistency. CLP has been applying RPA over the last few years to enhance customer experience and satisfaction, as well as uplift the internal workforce efficiency.
One of the success cases is the streamlined digital payment deferral request process. CLP Power understands the difficulties and hardship customers have been going through under the economic downturn and pandemic, and have therefore established an electronic submission channel to help customers make payment deferral requests. Upon receiving the electronic requests, the RPA will automatically handle the subsequent data processing, customer identity verification, eligibility validation, requests for approval, and notifications to the customers upon completion. These automated processes are handled by RPA without human intervention, providing a more timely and accurate service, while also enhancing employee productivity.
Since the implementation of this automated process, the RPA has processed over 45,000 payment deferral requests and the associated manhour savings have been re-deployed to provide other value-added services to our customers.